Building a Circular Economy with the Aim of Sustainable Growth
Mitsubishi Chemical Corporation
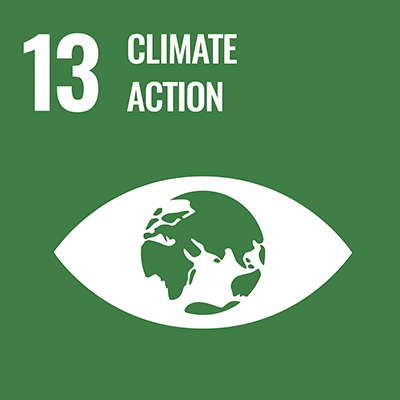
Relevant SDG
SDG 13: Take urgent action to combat climate change and its impacts
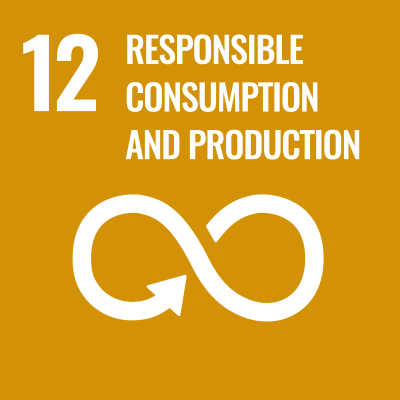
Relevant SDG
SDG 12: Ensure sustainable consumption and production patterns
Offering New Business Solutions by Pursuing a Circular Economy
Mitsubishi Chemical Corporation (MCC) is accelerating efforts to help realize a circular economy (CE) with a focus on plastic and carbon recycling. We aim to further grow our business by expanding the use of recycled plastics, converting to the use of biomass materials, promoting carbon recycling through biodegradation, and expanding our line of products that reduce GHG emissions from their use. Through the use of life cycle assessment (LCA) in quantitatively determining the environmental impact and carbon footprint of our products, we play a leading role in reducing environmental impact in various stages, including R&D, manufacturing, and product proposal. Furthermore, through open innovation and the establishment of recycling systems in cooperation with stakeholders, we are promoting efforts to realize a recycling-oriented society that contributes to more comfortable and secure lifestyles and the environment.
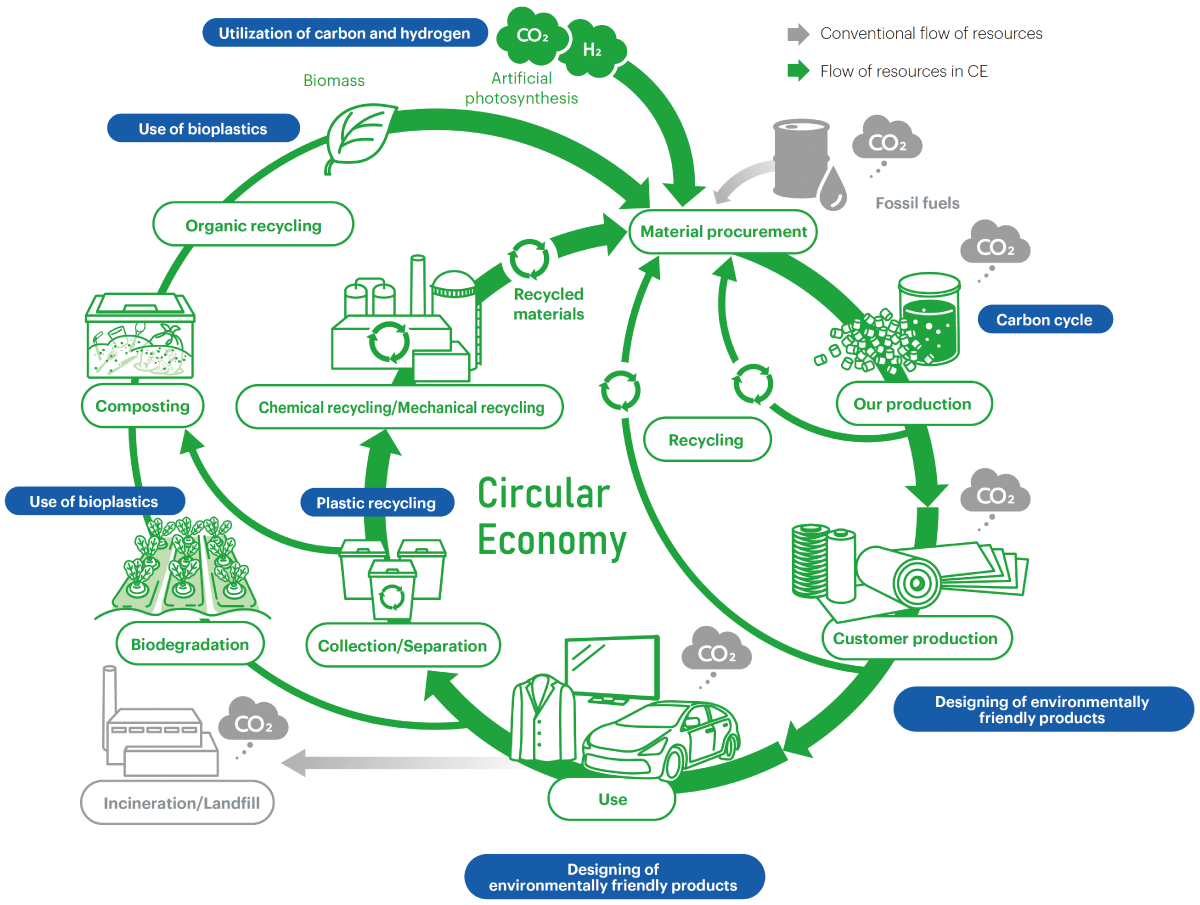
Plastic Recycling
- Establish a recycling model for mechanical recycling
- Consider business opportunities for chemical recycling
Use of Bioplastics
- Various plastics made from biomass
- Biodegradation
Utilization of Carbon and Hydrogen
Use of LCA
- Strengthen products and services that contribute to reducing environmental impact throughout the value chain
Open Innovation and Collaboration with Stakeholders
- Alliance To End Plastic Waste (AEPW)
- International Council of Chemical Associations (ICCA)
- Value Balancing Alliance (VBA)
- Global Impact Coalition (GIC)/
- Global Compact Network Japan (GCNJ)(in Japanese only)
- The University of Tokyo Center for Global Commons (CGC)(in Japanese only)
- Japan Clean Ocean Material Alliance (CLOMA)(in Japanese only)
- Japan Partnership For Circular Economy (J4CE)(in Japanese only)
- Carbon Recycling Fund Institute(in Japanese only)
Others
Advancing Partnerships to Build a Plastic Recycling Scheme
The recycling of waste plastics into raw materials can be divided into two categories: 1) mechanical recycling, in which the recovered waste plastics are turned into granular raw materials through a process in which they are physically crushed, and 2) chemical recycling, in which the recovered waste plastics are turned into oil, gas, and raw materials through a chemical decomposition process. MCC is working with partners in the value chain to develop, demonstrate, and commercialize technologies for both types of recycling according to the application. Traditionally, waste plastics were simply incinerated or landfilled, but we are developing and strengthening a system to recycle them into resources and raw materials. In addition, we have acquired International Sustainability and Carbon Certification (ISCC) PLUS for several of our production sites and products and are working to ensure traceability for recycled materials throughout the supply chain.
Mechanical recycling: Beverage label recycling
The Group’s proposal for the establishment of a resource recycling model to recycle beverage labels was accepted for a program for measures tackling marine plastic pollution conducted by Hiroshima Prefecture. We are introducing resource recycling (Label to Label*1) shrink sleeve labels to encourage consumers to recycle beverage labels, establishing a recovery scheme in the market, and verifying the stages (distribution, recovery, transportation, sorting, and recycling) through to the relabeling process. By conveying a meaningful message to consumers through the recycling of labels, we aim to establish technologies and develop a resource recovery scheme in communities.
- *1The resource-recycling (Label to Label) shrink sleeve label is manufactured by combining Fuji Seal, Inc.’s technology for removing printing ink and our film-forming technology.
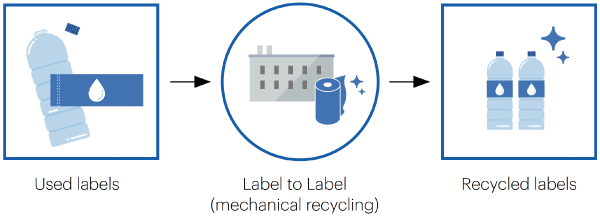
Chemical recycling: Recycling of waste plastics into oil
At our Ibaraki Plant, we are constructing a facility with ENEOS Corporation that will convert waste plastics into oil with an annual processing capacity of 20,000 tons, the largest of its kind in Japan. It is scheduled to commence operation in fiscal 2024. For the conversion process, we will install the supercritical water treatment technology from Mura Technology Limited of the United Kingdom, and the recycled oil will be used as a raw material in existing facilities, such as petroleum refineries and naphtha crackers, and will be reprocessed into petroleum products, chemicals, and various plastics. In addition, we will create a cycle for chemical recycling through alliances with other companies, such as our partnership with REFINVERSE, Inc. for stable procurement of waste plastics for raw materials.
We then plan to obtain certification for recycling chemicals using the mass balance approach*2 to prepare for establishment of a plastic chemical recycling plant and target widespread use of the mass balance method in society.
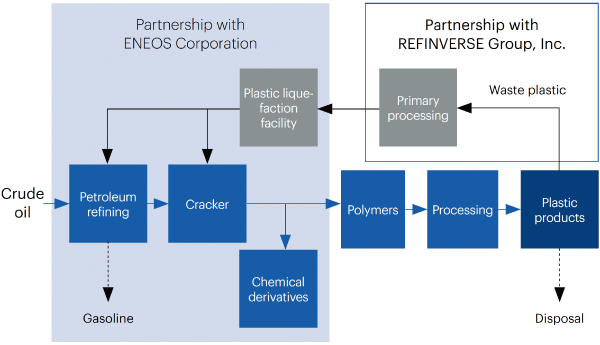
- *2Mass balance approach: A method of controlling a value chain in which a percentage of used recycled materials are voluntarily allocated to products by obtaining third-party certification for products manufactured by combining petroleum-derived raw materials and raw materials recycled from plastic waste.
MCC promises and declares that it will comply with the requirements for ISCC PLUS certification, under the latest International Sustainability and Carbon Certification (ISCC) rules.
Chemical Recycling: Recycling of acrylic resin
MCC and Mitsubishi Chemical Methacrylates Ltd. Have been investigating the recycling of polymethyl methacrylate (PMMA, or acrylic resin) for some time. In June 2021, we worked with Microwave Chemical Co., Ltd, our partner in investigating acrylic resin recycling technology, and built a new proof-of-concept (PoC) trial facility on the premises of its Osaka Plant. We are also performing a PoC trial in cooperation with the Japanese auto manufacturer, Honda Motor Co., Ltd. Tail lights and other parts made of acrylic resin are recovered from scrapped vehicles and recycled into raw material through thermal decomposition and refining using microwaves. This trial is verifying whether the raw material can be reused to produce acrylic resin for reuse in tail lights, without issues. At present, we have confirmed that acrylic resin produced through chemical recycling technology is transparent and performs at a level equivalent to conventional products.
We also expect the CO2 emissions from process of manufacturing chemically recycled products can reduce emissions by 70% compared to conventional products. This technology makes a substantial contribution to reducing CO2 emissions during manufacturing and the environmental impact, in addition to reducing the volume of waste acrylic resin.
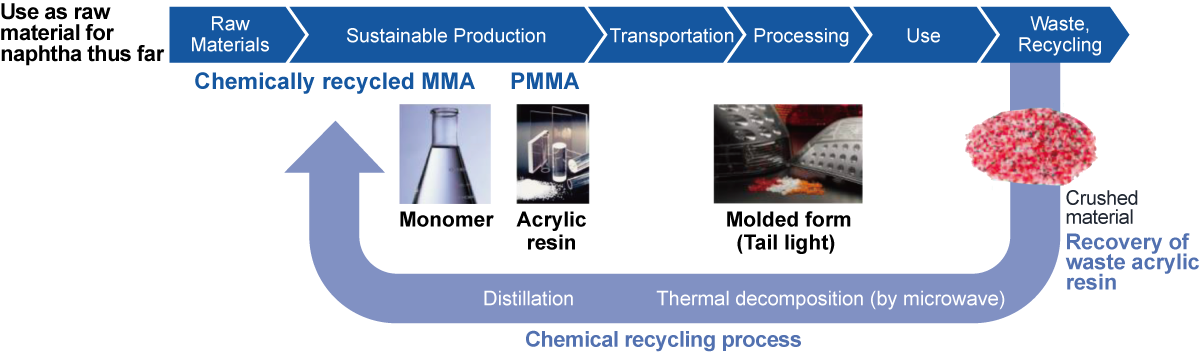
Reducing GHGs through an Artificial Photosynthesis Project
Artificial photosynthesis is a promising approach to reducing GHGs that uses CO2 emitted from power plants and factories as a raw material for chemical products. Since 2012, MCC has participated as a member of ARPChem,*3 a NEDO*4 project aimed at realizing artificial photosynthesis, and is involved in the development of core technologies for all of the following three processes.

1. A photocatalyst splits water into gaseous hydrogen and oxygen; 2. the hydrogen is then safely separated out of the mixed hydrogen and oxygen gas using a separation membrane; and 3. the hydrogen is used as a raw material together with CO2 recovered from the gas emissions of power plants or factories to produce chemical products.
The project’s target for photocatalyst solar energy conversion efficiency has been set at 10%. In fiscal 2019, an efficiency of 7% was achieved in a laboratory setting. Outdoor demonstrations of the water splitting systems began in fiscal 2020. Our proposal on Commercial Development of Artificial Photosynthesis-based Chemical Raw Material Production was selected as a Green Innovation Fund Project by NEDO in February 2022. This has advanced the artificial photosynthesis project into the next stage, aiming for practical implementation in communities. We will combine the petrochemical manufacturing technology and catalyst development technology we have developed thus far and will continue to pursue development of plastic manufacturing technology using CO2.
- *3ARPChem: Japan Technological Research Association of Artificial Photosynthetic Chemical Process, comprised of 11 member companies—INPEX CORPORATION, JX Advanced Metals Corporation, Dai Nippon Printing Co., Ltd., Dexerials Corporation, TORAY INDUSTRIES, INC., TOYOTA MOTOR CORPORATION, NIPPON STEEL CORPORATION, FURUYA METAL Co., Ltd., Mitsui Chemicals, Inc., Mitsubishi Chemical Corporation (MCC), and KYOCERA Corporation.
- *4NEDO: New Energy and Industrial Technology Development Organization
Establishing a Long-term Vision for the Chemical Industry
MCC and the Center for Global Commons (CGC) at the University of Tokyo have formed an industry-academia partnership with the aim of formulating a long-term vision of the chemical industry’s approach to sustainability with an eye toward society in 2050.
To ensure the sustainability of global environmental systems, CGC aims to scientifically demonstrate pathways for the fundamental transformation of socio-economic systems based on modelling and indices. In collaboration with a wide range of stakeholders, including private enterprises, CGC aims to drive this fundamental transformation through international cooperation.
MCC and CGC began joint research on April 1, 2021 to identify the social needs (particularly in the areas of products, services and social systems) of 2050, as well as those expected to emerge along the way by 2030 and 2040, and, given such needs, the role the chemical industry must play in protecting the Global Commons.*5
In September 2022, we published a report outlining the path toward net zero for the global chemical industry resulting from this joint research. The University of Tokyo subsequently published Planet Positive Chemicals in Japan (hereafter, “the Report”) on October 7, 2024 as the subsequent version. The newly published Report focuses on the chemical industry in Japan. It details the path for Japan’s chemical industry to achieve net zero in Scopes 1, 2, and 3 in quantitative terms. The Report also presents strategies and actions necessary to achieve net zero and make progress amid the many uncertainties such as future demand for net zero chemical derivatives and the appropriate manufacturing technology for them, in light of Japan’s strengths and weaknesses.
We will not keep these research results within our Group, but will share them widely with the public and will continue to pursue a new role in the chemical industry in a net zero world, as we build cooperative relationships with a broad range of partners.
- *5Global Commons: The global environmental system upon which the sustainable development of humankind is founded.