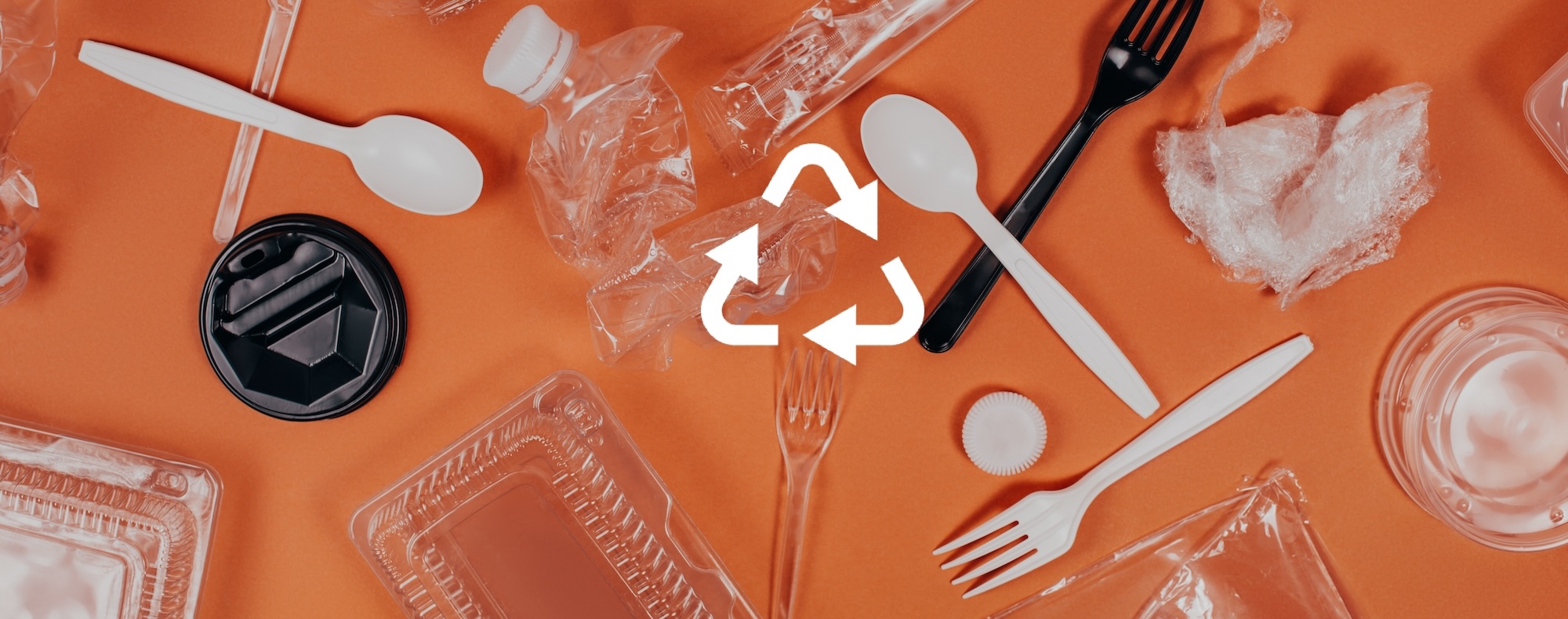
Chemical Recycling Through Plastic-to-Oil Conversion
A new resource recycling model using advanced technology
11/29/24
/ TEXT BY MCG
*The information mentioned in this article reflect the status at the time of publication.
The Mitsubishi Chemical Group (MCG Group) is promoting various kinds of chemical recycling methods as concrete solutions to the problem of plastic waste. We'll explain the chemical recycling method of plastic-to-oil conversion, jointly pursued by the MCG Group and ENEOS Corporation toward a circular economy, along with its advantages and challenges, and the potential for new resource recycling pathways.
What is chemical recycling through plastic-to-oil conversion?
Plastic-to-oil chemical recycling is a method to recycle used plastic by breaking it down to the raw material oil that can be reused as feedstock for new plastic. This process allows us to recycle mixed-material plastics, reducing the labor required for sorting. Additionally, it is possible to recycle them into high-quality chemicals that meet the same standards as brand-new products at existing manufacturing facilities.
Food packaging could serve as a good example demonstrating the potential of chemical recycling. There are very strict regulations on food containers and packaging that come into contact with people's mouths, limiting recycled waste plastics used for food containers and packaging. However, plastic-to-oil chemical recycling could expand the use of recycled materials in various areas, including food-related applications, where concerns about quality, safety and hygiene have restricted the use of recycled materials.
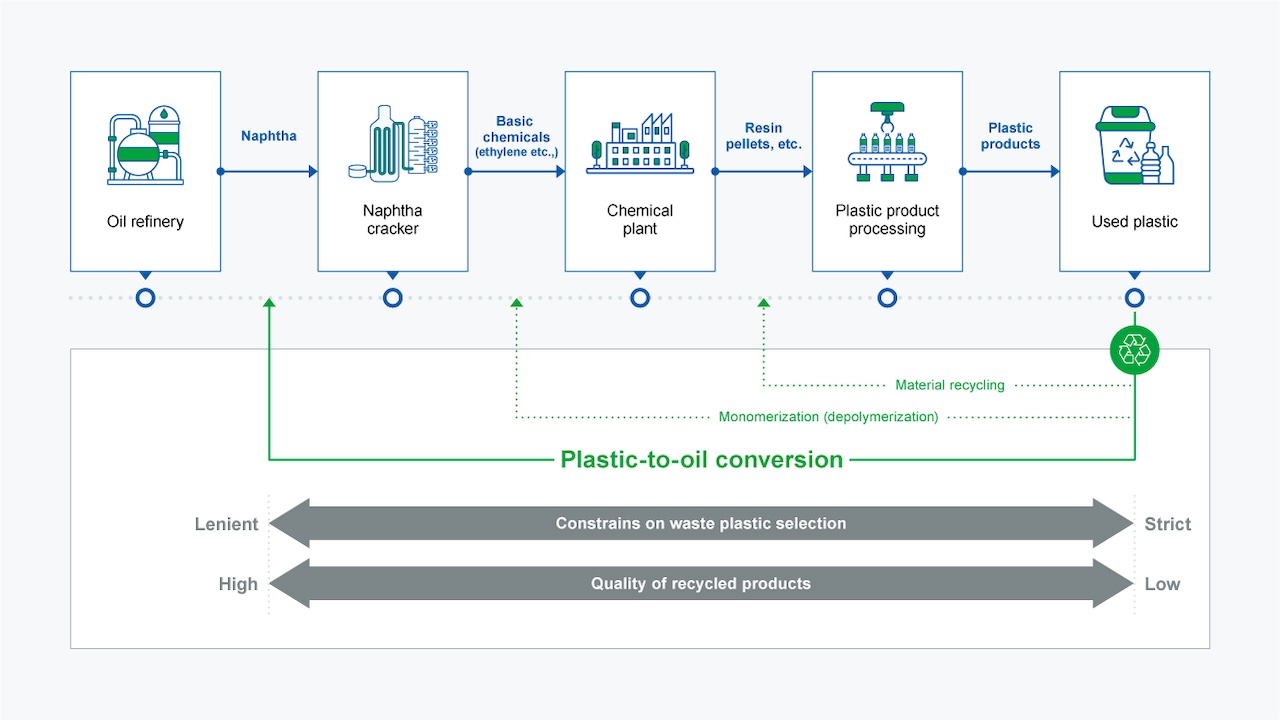
Oil conversion project in collaboration with ENEOS
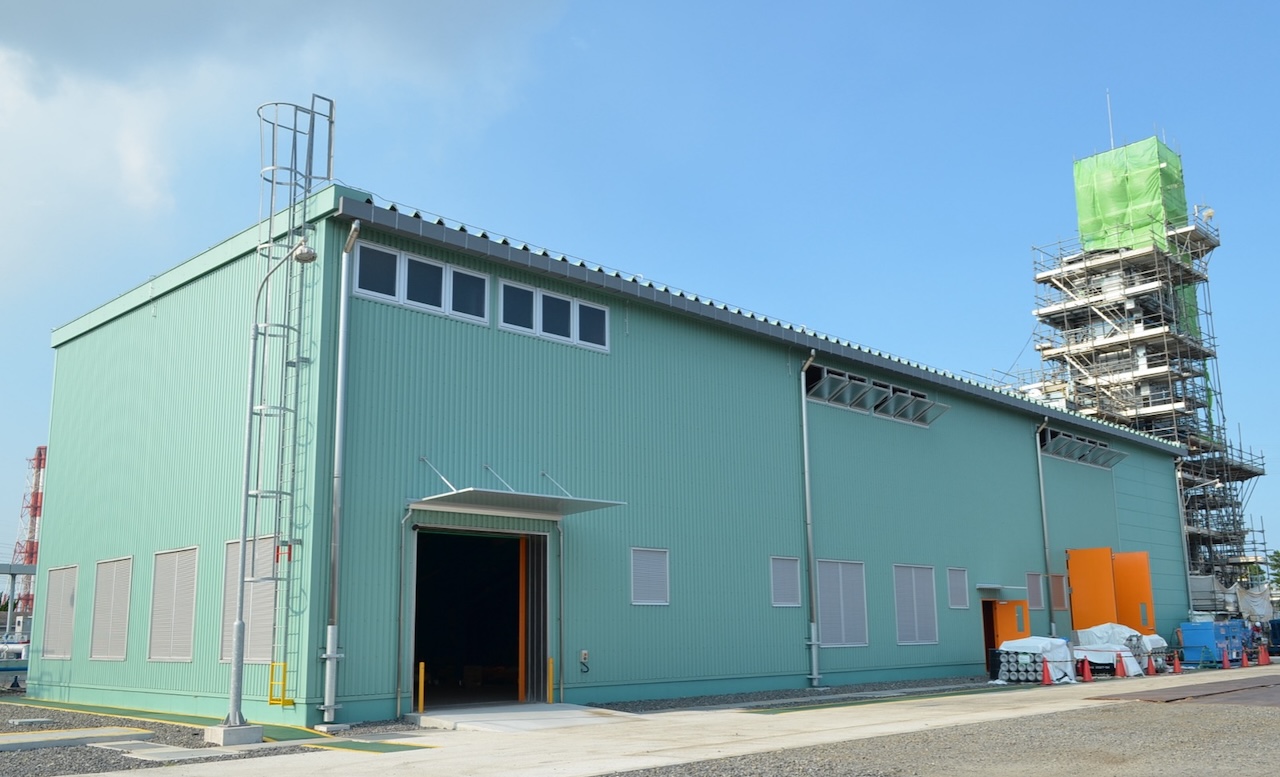
The MCG Group established a chemical recycling plant at the Ibaraki Plant in Kashima, in collaboration with ENEOS Corporation, to promote the plastics-to-oil conversion business. REFINVERSE Group, Inc. collects and procures used plastics as the raw materials for the chemical recycling plant. The recycled oil produced through chemical recycling is then used as a raw material in ENEOS’s oil refining facilities and the MCG Group’s naphtha crackers, where it is reprocessed into petroleum products and various chemical products. This new plant has one of the largest capacities in Japan, chemically processing 20,000 tons of waste plastics per year. Future plans include expanding the facility to handle larger volumes of waste plastics through scaled-up commercial operations.
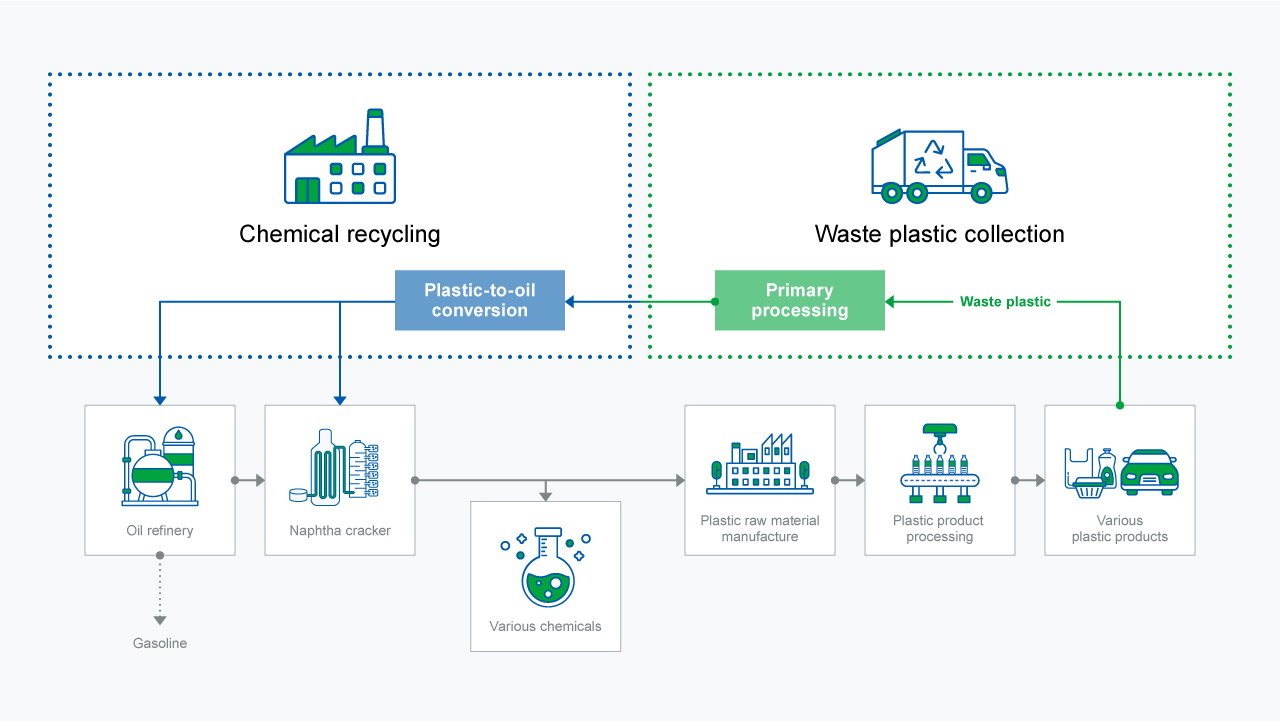
A new process utilizing advanced technology: supercritical water
We have introduced cutting-edge technology into the manufacturing process for plastic-to-oil chemical recycling. This innovative technology employs supercritical water under high temperatures and high pressure to break down plastics and convert them into oil. We have obtained a technology license from U.K.-based Mura Technology Ltd.
Recycling process with supercritical water
- Collect waste plastics, compress them into a molded state, and transport them to the plant
- Crush the plastics at the plant, melt them using an extruder, and apply pressure
- Break down the plastics into oil using supercritical water
- Separate the oil according to boiling point:
Naphtha-equivalent oil sent to the MCG Group, fuel-equivalent oil sent to ENEOS
- The MCG Group manufactures basic chemicals and derivatives, including ethylene and propylene
Advantages and challenges of oil conversion
The key advantage of this oil conversion technology is that it can use a mix of different types of waste plastics as raw materials and the recycled product can achieve the quality equivalent to new products (i.e., virgin materials). Another significant point is the high production efficiency; continuous operation allows continuous input of waste plastics. Furthermore, using supercritical water enables even application of heat, preventing the generation of gases due to excessive decomposition*1 and the generation of carbides from uneven heating, thus achieving a high yield. It is also characterized by high energy efficiency, as it can reduce uneven heating and lower the overall heating temperature.
Reusing waste plastics as chemical raw materials could lead to a significant reduction in fossil fuel consumption. While oil conversion helps prevent resource depletion, one challenge is that it requires a large amount of energy to induce the oil conversion reaction (via pyrolysis) even though it is energy efficient. However, comparing over the entire lifecycle, this process emits less GHG than incinerating waste plastics.*2 Plastic-to-oil conversion is a promising approach to recycling waste plastics, through further technological development is required to improve energy efficiency.
It is also important to establish a system for stable collection of waste plastics to be used as raw materials. Currently, only about 9% of the world's waste plastics are recycled.*3 The MCG Group is working with companies throughout the supply chain, such as REFINVERSE, to establish a scheme for efficient and stable collection of waste plastics.
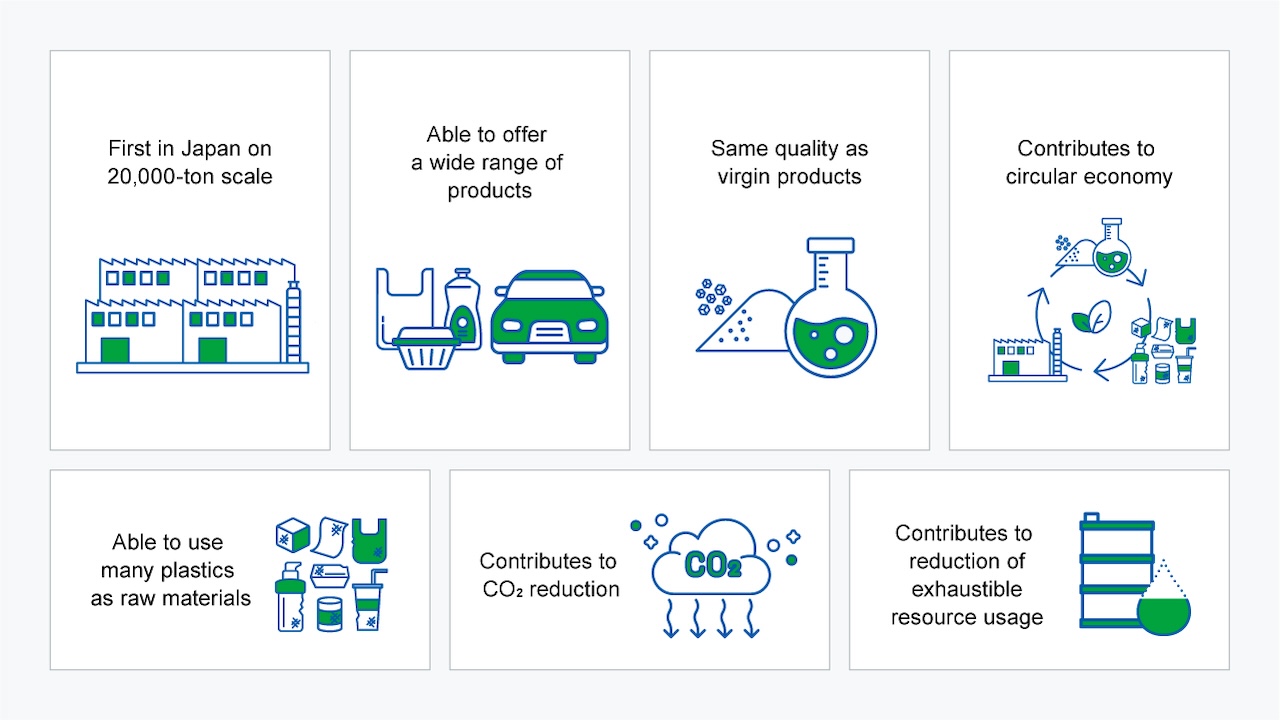
Toward the realization of a circular economy for true resource recycling
In recent years, plastic recycling regulations have become strengthened, particularly in Europe, and it is anticipated that targets and rules for higher usage rates of recycled plastic will be established in the future.
As a method of recycling waste plastics, we can expect an expansion in material recycling. Meanwhile, chemical recycling, which is an innovative form of recycling, is a promising solution for the next generation, This technology can recycle used plastic, which have previously been incinerated or disposed of without being recycled, into products that are just as good as new materials. In addition to conventional material recycling, by introducing various chemical recycling technologies, the MCG Group will proactively address waste plastics challenges that industries such as food and automotive are facing and contribute to the realization of a recycling-oriented society.
- *1 Excessive decomposition refers to the breakdown of a substance beyond the necessary level. When breaking down materials, it is important to stay within an appropriate range, but if the heating is too strong or the temperature is uneven, excessive decomposition may occur, leading to the generation of unwanted gases and carbides and lower quality.
- *2 The comparison is between incinerating waste plastics made from petroleum-derived oil products, using the resulting energy to generate electricity, and collecting waste plastics for chemical recycling to produce oil products.
- *3 Source is OECD Global Plastics Outlook Database